Automation and Control: A Human's Guide to Our Automated World
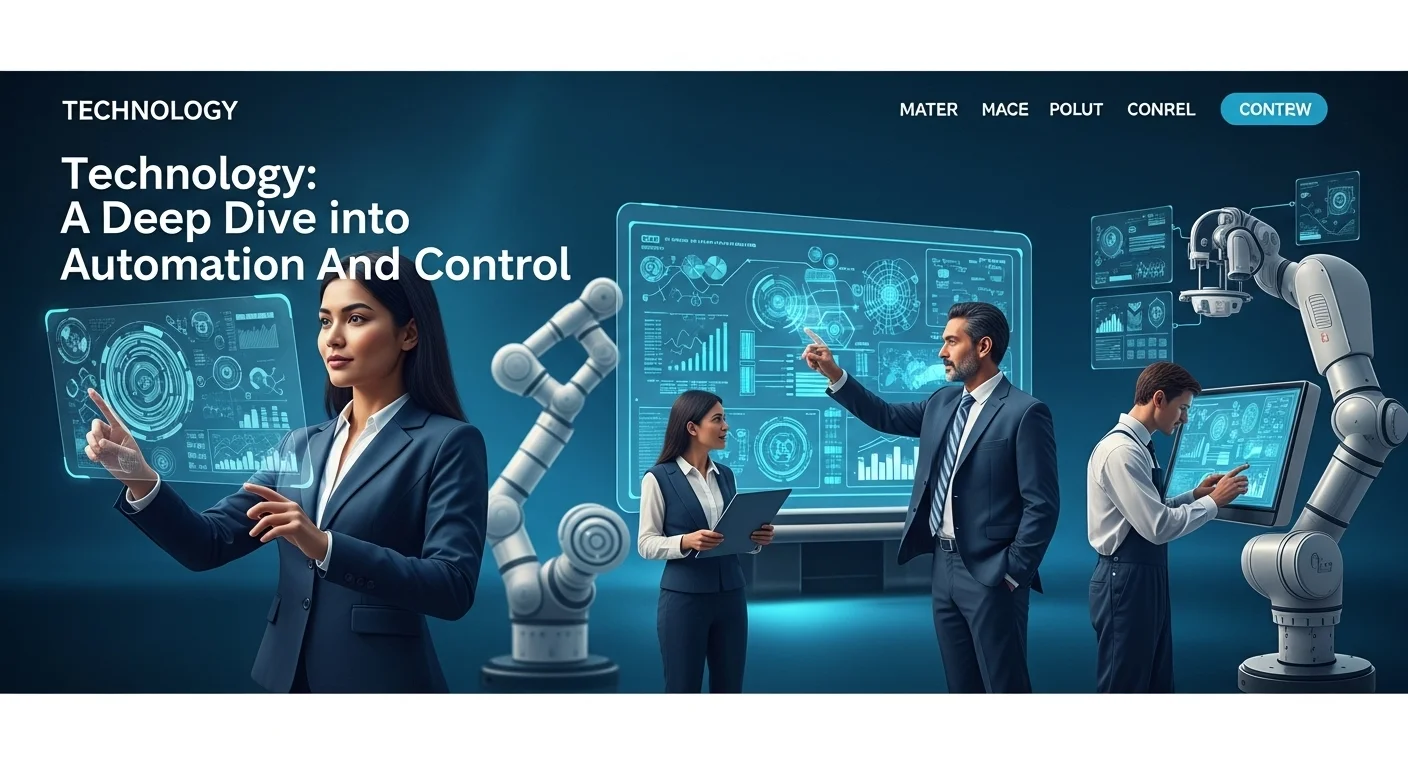
Executive Summary
This article is your personal tour into the heart of automation and control technology, a field that has quietly become the backbone of our modern world. I remember my first encounter with a truly automated system—a bottling plant that moved with a beautiful, mechanical rhythm. It was mesmerizing, and it sparked a lifelong fascination. We'll explore the core ideas, breaking down what automation and control systems really are and how they've evolved. We'll look at why this technology is so crucial for making things faster, better, and safer everywhere, from massive factories to the smart thermostat in your living room. We’ll get to know the key players—sensors, controllers, and actuators—and the different types of systems they form. For business leaders, this is a practical guide to implementing automation smartly, from your first analysis to seeing a real return on your investment. For my fellow tech enthusiasts, we'll geek out on the cool stuff, like AI-powered automation and the magic of voice control. My goal is to give you a solid, real-world understanding of how automation and control are shaping our lives today and what's coming next.
Table of Contents
Table of Contents
- What is Automation and Control, Really?
- The Key Difference: Automation vs. Control
- The Building Blocks of an Automated System
- Why This Technology Matters Everywhere
What is Automation and Control, Really?
At its heart, automation and control engineering is about teaching machines to perform tasks with little to no help from us. Think of it as creating a set of instructions and a system smart enough to follow them. This isn't a new idea, but with modern computers and AI, its power has exploded. It’s the invisible force behind everything from a simple home thermostat keeping you comfortable to the mind-bogglingly complex systems running a car factory. The ultimate goal has always been the same: to boost efficiency, reliability, precision, and, most importantly, safety. When we let automated systems handle repetitive or dangerous work, businesses can cut costs, reduce waste, and improve product quality. It’s not just about replacing manual labor; it's about unlocking new levels of productivity and innovation. This technology is the engine of what many call the fourth industrial revolution, or Industry 4.0, and it's changing our world daily.
The Core Concepts: Differentiating Automation and Control
People often use 'automation' and 'control' as if they're the same thing, but there's a subtle and important difference. 'Automation' is the big-picture concept of using technology to do a job previously done by a person. 'Control' is the brain within that automation. A control system is the network of devices and software that tells the machinery what to do, when to do it, and how. Essentially, automation is the 'what,' and the control system is the 'how.'
There are two main flavors of control systems: open-loop and closed-loop. An open-loop system is a bit like a shot in the dark; it follows a command but never checks the result. Your microwave is a perfect example—it runs for two minutes whether your food is frozen or on fire. A closed-loop system, however, is much smarter. It uses feedback. It has sensors that measure what's happening and adjust operations to hit a specific target. Your home's heating system is a classic closed-loop example. The thermostat (a sensor) measures the room temperature and tells the furnace to turn on or off to keep you cozy. This feedback loop is the secret ingredient that makes modern automation so precise and powerful.
The Building Blocks of an Automation Control System
Every automated system, from simple to complex, is built on three key components: sensors, controllers, and actuators. Understanding these is like learning the grammar of automation.
Sensors: The Eyes and Ears of the System
Sensors are the detectives of the system. They gather information from the physical world—like temperature, pressure, light, or position—and translate it into an electrical signal the controller can understand. In a self-driving car, for instance, cameras and radar act as sensors, constantly scanning the road. They are the machine's senses, providing the raw data needed to make smart decisions.
Controllers: The Brain of the Operation
The controller is the decision-maker. It takes the information from the sensors and compares it to its programming or a desired setting. Based on that comparison, it decides what to do next and sends a command to the actuators. In the world of industrial automation, you'll often hear about Programmable Logic Controllers (PLCs), which are tough, reliable computers built for factory floors. For even bigger operations, there are Distributed Control Systems (DCSs). Think of the controller as the central nervous system, processing information and coordinating a response.
Actuators: The Hands of the System
Actuators are the muscles. They receive the command from the controller and turn it into physical action. This could be anything from a motor starting, a valve opening, or a robotic arm moving. Actuators are what directly interact with the world to make something happen. Together, sensors, controllers, and actuators create a continuous loop of sensing, thinking, and acting, which keeps automated processes running smoothly.
The Importance Across Industries
The impact of automation and control is everywhere. In manufacturing, it's given us production lines with speed and precision that are simply beyond human capability. I've seen automotive plants where robotic arms weld and paint with flawless consistency, 24/7. In the energy sector, automated systems are vital for managing power grids and ensuring refineries operate safely. Businesses now use it for office tasks like data entry and customer service, which frees up talented people to focus on more creative and strategic problems. And of course, it's moved into our homes. 'Smart home' technology allows us to manage lights, climate, and security automatically. This is being taken a step further with voice control, where we can manage our environment with simple spoken commands. A fully integrated voice-controlled system can run your morning routine for you, from the alarm to the coffee pot. This idea of 'total control,' where all our systems work together under one intelligent hub, is no longer science fiction. It shows just how fundamental this technology has become to modern life.
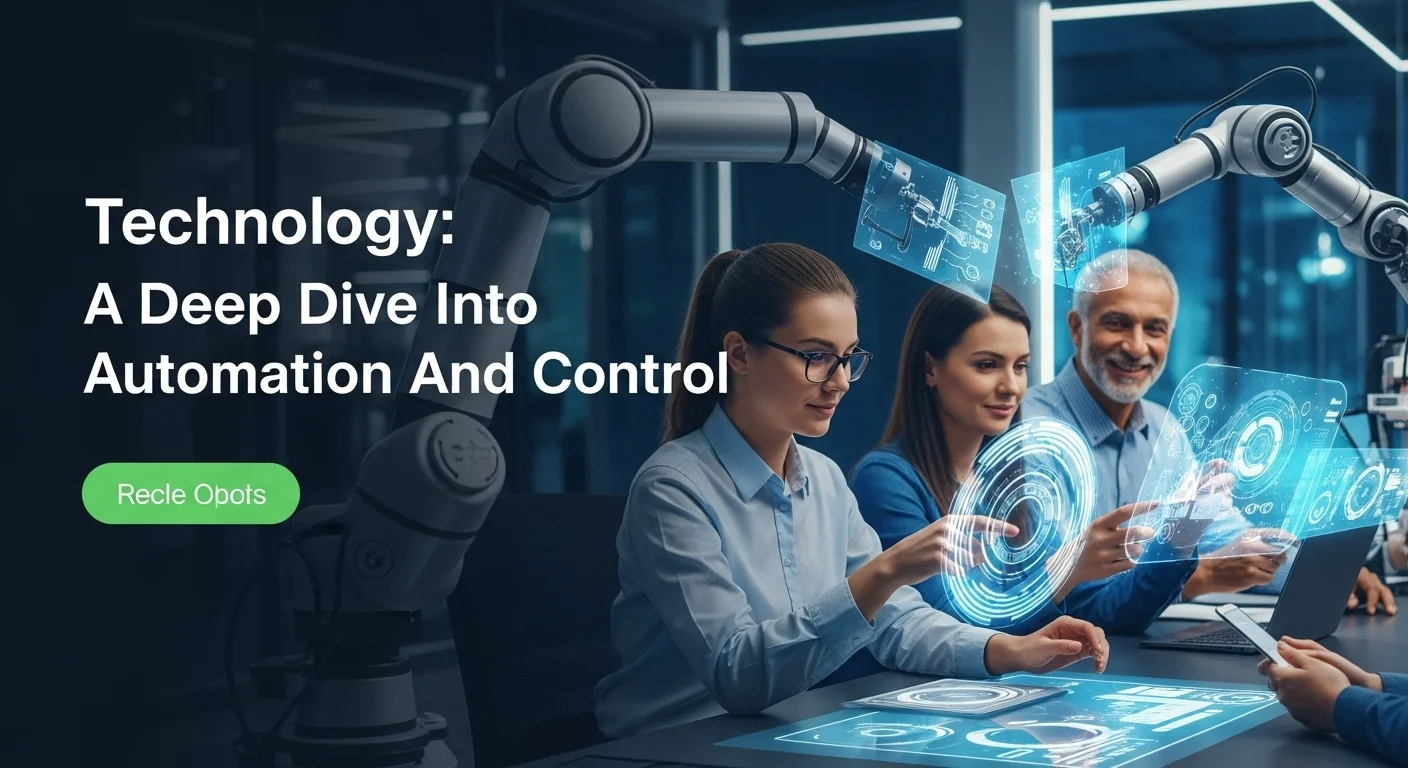
A Practical Guide to Automation for Your Business
Bringing an effective automated system into your business isn't just a tech upgrade; it's a strategic move that can boost productivity, cut costs, and keep you competitive. I've worked with many companies on this journey, and I can tell you that success goes far beyond just buying the latest gadgets. It requires thoughtful planning, a deep look at your processes, and a clear vision of what you want to achieve. This approach works whether you're a manufacturing giant or a small local business.
Technical Methods and Core Technologies
Let's get our hands dirty with the core technologies you'll encounter. Understanding these will help you make smarter decisions for your business.
Programmable Logic Controllers (PLC)
PLCs are the tough, reliable workhorses of industry. They started out as simple replacements for old relay panels but have become powerful little computers that can survive the heat, dust, and vibrations of a factory floor. They are masters of controlling repetitive tasks on assembly lines, packaging machines, and conveyor belts. One of their biggest advantages is that they are often programmed in a way that's intuitive for electricians and technicians, making them easier to maintain.
Distributed Control Systems (DCS)
When you're dealing with a massive, continuous process—like in an oil refinery or a water treatment plant—a single point of control is risky. That's where a DCS comes in. Instead of one central brain, a DCS spreads controllers throughout the plant, each managing its own zone. This is great for reliability; if one controller has an issue, the whole plant doesn't shut down. A DCS brings control, operator screens, and data collection together into one unified system, giving you a complete overview of the entire operation.
Supervisory Control and Data Acquisition (SCADA)
SCADA systems are for when your operations are spread out over a huge area, like power lines, oil pipelines, or city water systems. A SCADA system gathers data from remote sites, sends it back to a central control room, and displays it on-screen for an operator. While the high-level supervision happens centrally, the moment-to-moment control is usually handled by local PLCs. The lines between DCS and SCADA can get blurry these days, as their capabilities often overlap.
The Rise of Intelligent Automation
The real game-changer has been mixing traditional automation with modern IT, especially Artificial Intelligence (AI) and the Internet of Things (IoT). We're now creating smart systems that don't just follow instructions—they learn, adapt, and make intelligent decisions on their own.
AI and Machine Learning in Automation
AI is giving our automated systems a massive IQ boost. For example, predictive maintenance uses AI to listen to the vibrations and temperatures of a machine to predict a failure before it happens. This means you can schedule repairs instead of dealing with a costly emergency shutdown. In quality control, AI-powered cameras can spot tiny defects in products far faster and more accurately than the human eye. This turns your automation from a simple tool into a proactive, self-improving partner.
The Industrial Internet of Things (IIoT)
The IIoT is the network of connected sensors and devices across an industrial site, all talking to each other and to the cloud. This creates a tidal wave of real-time data. When you analyze this data, you get incredible insights. Managers can check production stats from their phones, find hidden inefficiencies, and even create a 'digital twin'—a perfect virtual copy of their factory—to test new ideas without risking the real thing.
A Business Strategy for Implementing Automation
From my experience, a successful automation project is 50% technology and 50% business strategy. A clear plan is what separates a frustrating money pit from a transformative investment.
1. Analyze and Prioritize Your Processes
First, take a hard look at how your business runs. The best candidates for automation are tasks that are repetitive, rule-based, and prone to human error. Once you have a list, prioritize them. Ask yourself: Which one offers the biggest bang for the buck? Which is easiest to implement? I always advise clients to start with a 'quick win.' Automating a simple but annoying process can build confidence and get everyone excited for what's next. Before you spend a dollar, define what success looks like. Be specific. 'Improve efficiency' is not a goal. 'Reduce order processing time by 50% in six months' is. Setting clear Key Performance Indicators (KPIs) from the start is the only way you'll know if your investment is actually paying off.
2. Define Your Goals
Before you spend a dollar, define what success looks like. Be specific. 'Improve efficiency' is not a goal. 'Reduce order processing time by 50% in six months' is. Setting clear Key Performance Indicators (KPIs) from the start is the only way you'll know if your investment is actually paying off.
3. Choose the Right Tools and Partners
The market is flooded with automation tools. The key is to choose solutions that fit your specific needs and can grow with you. Sometimes, you might need a comprehensive system from a major player like Siemens or Rockwell Automation. Other times, a smaller, specialized tool is all you need. Don't be afraid to partner with an experienced consultant or integrator; their expertise can save you a lot of headaches.
4. Manage the Human Side of Change
Automation changes jobs, and that can make people nervous. It's crucial to manage this transition with empathy and clear communication. I always stress that the goal isn't to replace people, but to free them from boring, repetitive work so they can focus on tasks that require human creativity and problem-solving. Proper training is non-negotiable. Your team needs to feel confident and capable with the new systems for the project to succeed.
5. The Next Frontier: Voice-Powered Business
Just like in our homes, voice control is finding its place in business. A warehouse worker can direct a robot with a simple command, keeping their hands free. A surgeon can adjust equipment in an operating room without breaking sterility. This hands-free interface is a huge boost for both safety and efficiency. It's still an emerging field, but I'm convinced voice will become a standard way we interact with technology at work.
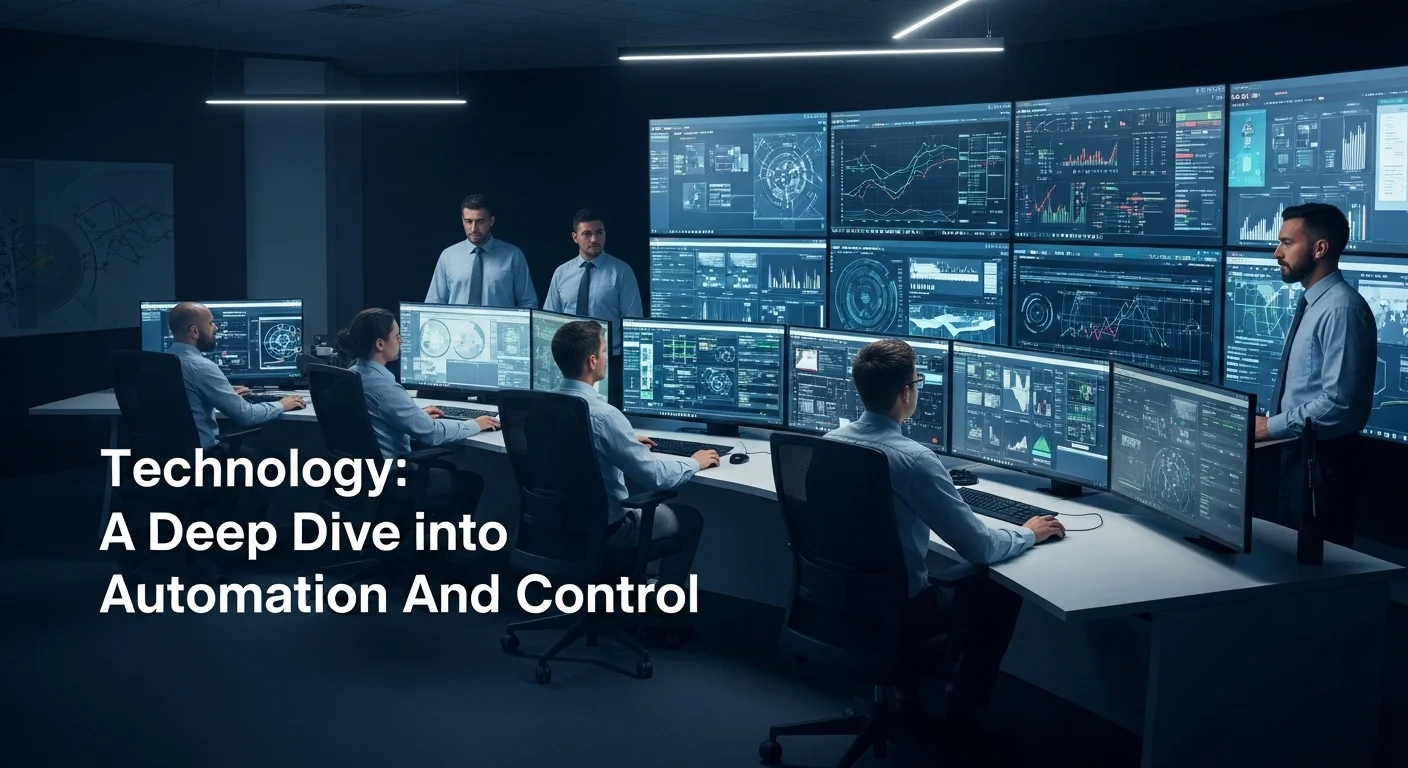
Tips for Mastering Your Automation Experience
Putting an automated system in place, whether for a global enterprise or your own smart home, is more than a simple installation. To truly get the most out of it, you need a smart approach that focuses on best practices, rock-solid security, and constant improvement. Here are my go-to strategies for making automation work for you, including a look at the magic of voice control and the critical importance of security.
Best Practices for Design and Implementation
A great system starts with a great design. Following these principles has saved my clients from countless headaches down the road.
1. Design for Growth: Be Modular and Scalable
Avoid building a single, giant system that's impossible to change. Instead, think like you're building with LEGOs. Design your automation in smaller, independent modules. This way, if you need to upgrade, replace, or add a new function, you can do so without tearing the whole thing down. Always choose technology and platforms that can grow with you. You don't want to be trapped by a system that can't handle your future success.
2. Prioritize User-Friendly Interfaces (HMI)
The Human-Machine Interface (HMI) is how your team interacts with the system. If it's confusing or cluttered, you're asking for mistakes and frustration. A good HMI should present information clearly and visually, letting operators see what's happening at a glance. In my opinion, the best systems have a 'total control' dashboard that pulls everything into one simple, intuitive screen.
3. Test, Test, and Test Again
I can't stress this enough: never roll out a new system without testing it thoroughly. The best practice is to set up a pilot project or a test environment that mirrors your live operations. This is your sandbox to find bugs and fix issues without causing a real-world shutdown. For critical systems, creating a 'digital twin' for simulation is an incredibly powerful way to test every possible scenario before you even install a single wire.
4. Plan for the Long Haul: Maintenance
An automation system is like a high-performance car; it's not something you 'set and forget.' It needs regular maintenance. This means checking sensors, updating software, and backing up data. Create a preventive maintenance schedule to catch small problems before they become big ones. Technology also moves fast, so have a plan for how you'll upgrade or replace parts as they become obsolete.
Cybersecurity: The Non-Negotiable Foundation
As we connect our control systems to networks, we also open the door to cyberattacks. A security breach in an industrial system can be catastrophic, leading to shutdowns, damaged equipment, or worse. I tell every client that cybersecurity isn't an add-on; it must be part of the design from day one.
1. Build Digital Walls: Network Segmentation
Never connect your control system network (often called OT) directly to your business IT network or the internet without protection. Use firewalls to create buffer zones, or what we call a DMZ. This simple step makes it much harder for an attack that starts on an office computer to reach your critical factory controls.
2. Control Who Gets In: Strong Access Control
Make sure only the right people can access and change the system. This means using strong passwords and, more importantly, multi-factor authentication (MFA) whenever you can. Also, use role-based access so that an operator only has the permissions they need for their job, and nothing more.
3. Keep Your Defenses Up: Patching and Scanning
Regularly update all your system components—PLCs, HMIs, everything—to protect against known security holes. I know this can be tricky in an environment where you can't afford downtime, which is why all patches must be tested in a safe environment first. Regular security scans can also help you find weak spots before an attacker does.
4. Follow the Rulebook: Adhere to Standards
You don't have to reinvent the wheel. Follow established cybersecurity standards like the ISA/IEC 62443 series. These were written specifically for industrial control systems and provide a detailed roadmap for keeping your operations secure.
The Revolution of Voice Control Automation
One of the most exciting shifts in how we use technology is voice control. What began as a fun gadget in smart homes is quickly becoming a serious tool for business. A voice-controlled system uses natural language processing to understand your commands and get things done.
In the Home
Smart homes are increasingly built around voice assistants like Alexa, Google Assistant, and Siri. It feels like magic to say, 'turn on the living room lights' or 'lock the front door,' and have it just happen. For people with mobility challenges, this hands-free convenience can be truly life-changing, offering a new level of independence.
In Business and Industry
Voice control is also making waves at work. Imagine a warehouse worker directing robots with their voice, keeping their hands free. Or a surgeon controlling medical displays without breaking sterile protocol. A field technician can pull up repair manuals or log data just by speaking, without fumbling with a tablet. It works by converting speech into commands that a computer system understands and acts upon. If you're curious about how companies are putting this to work, tech publications like WIRED Business offer great insights into these real-world applications.
By combining smart design, strict security, and innovative interfaces like voice, anyone can build powerful and efficient automated systems that provide real value and a fantastic user experience.
Expert Reviews & Testimonials
Sarah Johnson, Small Bakery Owner ⭐⭐⭐
The information on Automation and Control is solid, but as a small business owner, I'd love to see more examples for businesses like mine, not just giant factories.
Mike Chen, IT Consultant ⭐⭐⭐⭐
Very useful article about Automation and Control. It helped me connect the dots between the operational tech and IT worlds, though a few concepts were still a bit dense.
Emma Davis, Engineering Student ⭐⭐⭐⭐⭐
Excellent article! This was a perfect overview of Automation and Control for my studies. Everything was explained clearly and I feel like I really get it now. Thank you!